The Secret to Low Carbon Housing Developments - Less is More
Andrew Leiper
Net Zero Carbon Leader and Principal Engineer
Max Fordham LLP
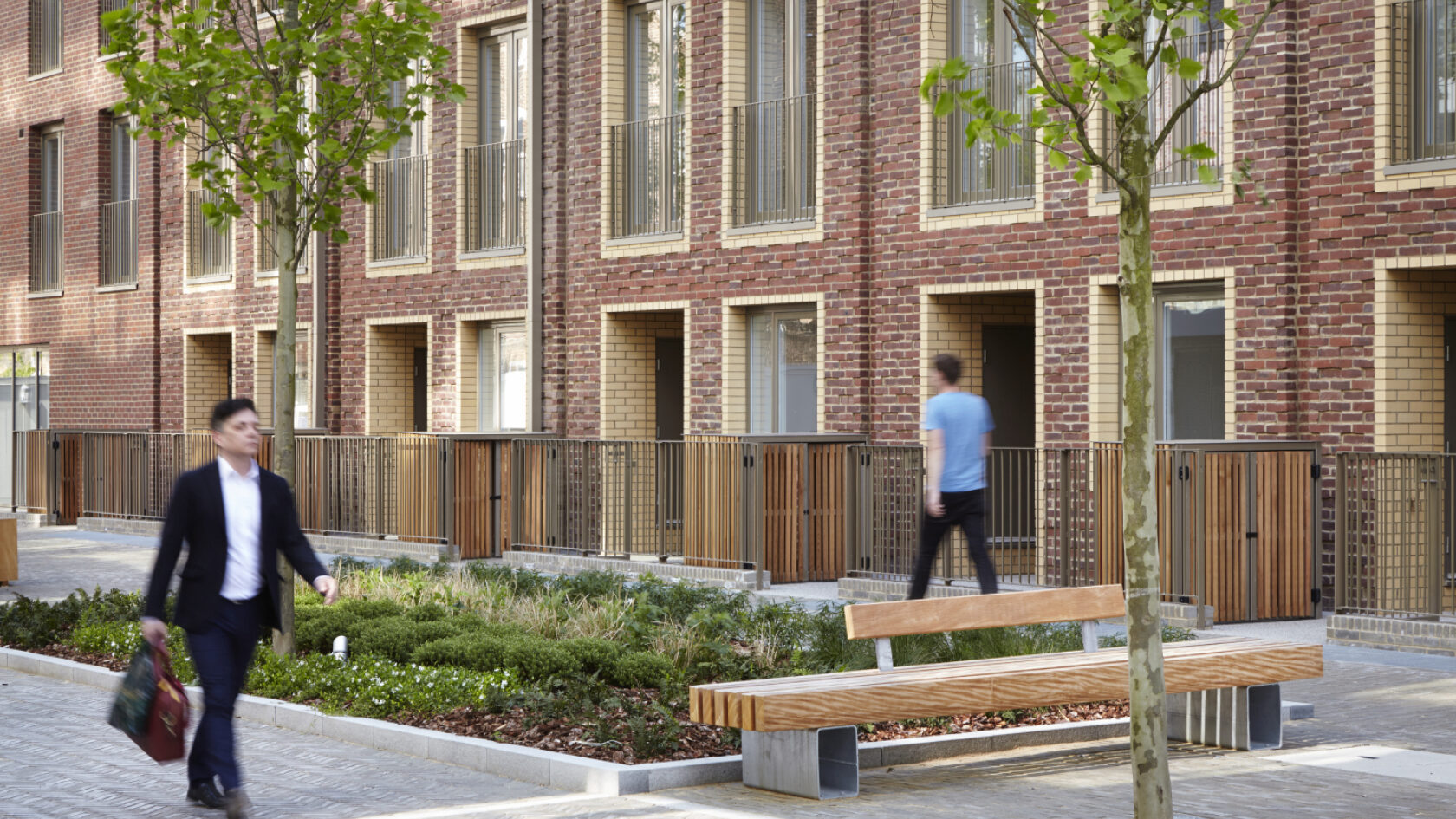
Reducing the amount of carbon – both embodied and operational - in our buildings is the single-most critical issue facing the built environment. It’s greatly encouraging that in recent years this has become a mainstream issue, not just for the construction sector, but for society as a whole. For sustainable engineers and those involved in the design of buildings, we have been grappling with this problem for some time. However, the answer at a basic level has never changed: less is more.
When building new homes, the production, transport, and construction of materials emits carbon. For building services specifically, the accounting of embodied carbon is generally poor, as systems and equipment are made up of components and composite materials that can’t be simply measured by weight or volume. However, it still holds that using fewer materials in a development will result in an inherently lower carbon footprint.
There are many ways to minimise the amount of materials in a development. All require an early conversation, then continued commitment from the client and design team throughout the design and construction process. There can be a tendency to initially start with the architectural design and consideration of other constraints, which usually makes implementing sustainable solutions harder, so making upfront decisions to use less “stuff” will keep things simple whilst also leading to a cleaner, easier and generally better appreciated design that’s more environmentally sustainable. Less building services also means a more cost-effective and less wasteful development, both during construction and when in-use.
On a recent residential project of 30 two-storey units, Max Fordham found that rearranging the interior layout by moving the utility cupboard to share drainage with the WC and situating the bathroom above the kitchen allowed for the utilities to be incorporated into the design much more efficiently. Overall, there was a reduction of about 10 metres of UPVC pipework taking around 28.9Kg CO₂ out of the development, per home.
Similar economies can be applied to ventilation systems. For example, the installation of MVHR (Mechanical Ventilation with Heat Recovery) units in external walls, to allow for a simpler layout of ventilation ductwork, dramatically reduces the amount of ductwork needed. Our analysis has found that designs that can reduce the amount of ductwork by greater than 50% lead to potential savings of 31.8 Kg CO₂ plus a further saving of 11 Kg CO₂ because less polystyrene insulation is needed, as the ductwork connects to the outside directly. Less ductwork also means less resistance, so fans are quieter and use less energy, therefore reducing operational carbon.
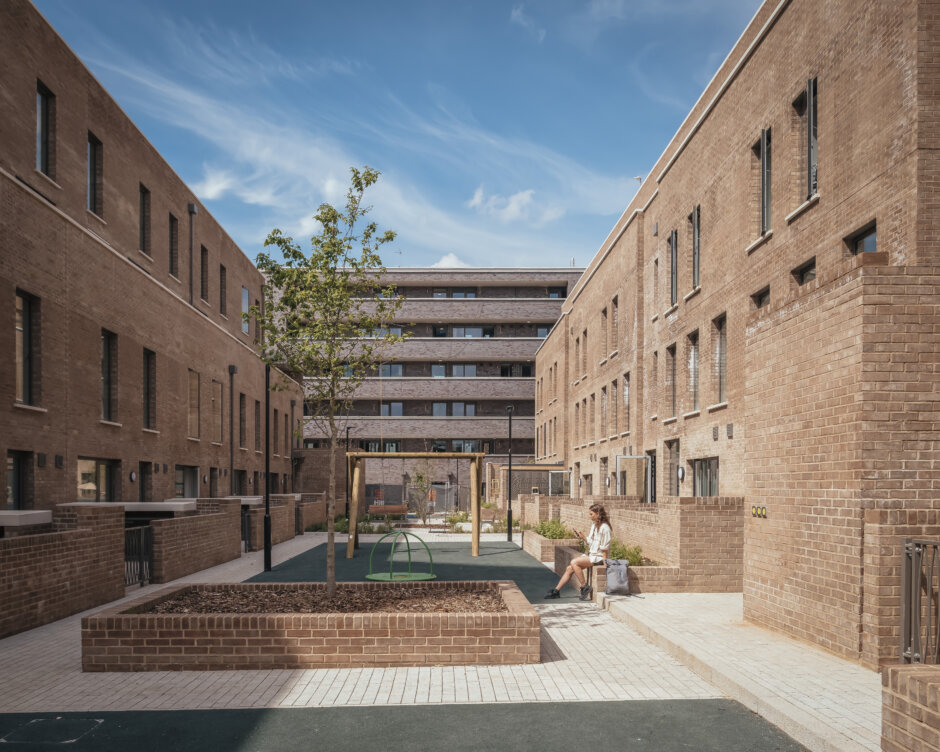
- Have early conversations about ways to reduce materials, energy and duration of the build.
- Look for opportunities to centralise mechanical, electrical and ventilation installations, and exploit the repeatability of systems.
- Rationalise components, limit sizes and options, and remove dependency upon physical configurations. This will mean that less materials are used, deliveries can be made in bulk, so transport emissions and packaging waste are also significantly reduced. Design from standard kits and parts, to allow the economies of scale to come through.
- Commit to the vision and hold on to early decisions. Don’t allow them to become eroded as a project develops.
This article was originally published in Housing Today in June 2021.